Generator Maintenance: Preventive, Predictive & Corrective Approaches
- elearning@ensemble
- Mar 2
- 2 min read
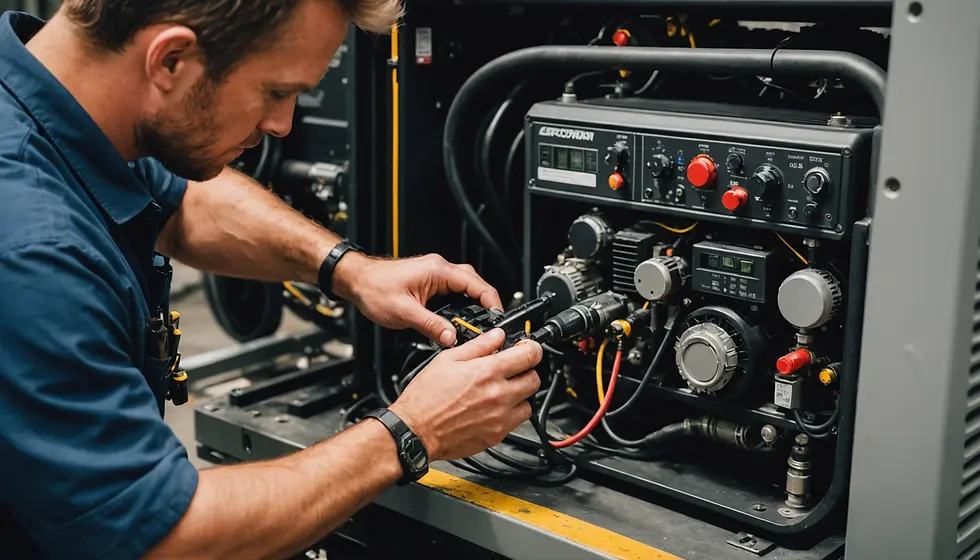
Regular generator maintenance is essential to ensure uninterrupted power supply, extended equipment lifespan, and cost-effective operation. A well-maintained generator prevents unexpected failures, costly repairs, and regulatory non-compliance.
This blog explores the three primary generator maintenance approaches: preventive, predictive, and corrective maintenance, along with best practices for optimal generator performance.
1. Preventive Maintenance (Scheduled Inspections & Servicing)
Preventive maintenance (PM) involves regularly scheduled inspections and servicing to prevent potential failures before they occur.
1.1 Key Preventive Maintenance Tasks
✅ Fuel System Inspection – Check fuel levels, drain water from the fuel tank, and clean fuel filters.
✅ Lubrication System Check – Monitor engine oil levels, replace oil & filters periodically.
✅ Battery & Electrical System Inspection – Ensure batteries are fully charged, and connections are secure.
✅ Cooling System Maintenance – Inspect radiators, coolant levels, and hoses for leaks.
✅ Exhaust System Check – Ensure exhaust pipes are secure and free from blockages.
✅ Load Bank Testing – Periodically test the generator under full load conditions.
1.2 Preventive Maintenance Schedule
Task | Frequency |
Battery Check | Weekly |
Oil & Coolant Level Check | Bi-Weekly |
Fuel System Inspection | Monthly |
Load Bank Testing | Quarterly |
Full Engine Overhaul | Annually |
✔ Following a structured PM plan reduces sudden failures and extends generator life.
2. Predictive Maintenance (Condition-Based Monitoring)
Predictive maintenance (PdM) uses real-time data analysis and monitoring technologies to predict failures before they happen.
2.1 Key Predictive Maintenance Techniques
🔹 Vibration Analysis – Detects mechanical wear in bearings, alternators, and engine mounts.
🔹 Infrared Thermography – Identifies hot spots in electrical circuits to prevent insulation failures.
🔹 Dissolved Gas Analysis (DGA) – Monitors oil and fuel contamination for early fault detection.
🔹 Load & Performance Monitoring – Tracks generator load trends to prevent overloading issues.
✔ PdM is a cost-effective approach that minimizes unplanned downtimes.
3. Corrective Maintenance (Troubleshooting & Repairs)
Corrective maintenance (CM) is performed when a generator fails unexpectedly due to mechanical or electrical issues.
3.1 Common Generator Issues & Solutions
Issue | Possible Cause | Solution |
Failure to Start | Dead battery, faulty starter | Charge/replace battery, check starter |
Low Voltage Output | Faulty AVR, fuel issues | Inspect AVR, clean fuel injectors |
Overheating | Clogged radiator, low coolant | Clean radiator, refill coolant |
High Fuel Consumption | Fuel leaks, worn injectors | Fix leaks, replace injectors |
✔ Timely corrective maintenance ensures quick recovery from failures.
4. Best Practices for Generator Maintenance
🔹 Follow a structured maintenance schedule (PM, PdM, CM).
🔹 Use genuine spare parts for repairs and servicing.
🔹 Conduct monthly load tests to verify generator capacity.
🔹 Maintain a detailed logbook for maintenance history tracking.
Wrapping Up
Effective generator maintenance—whether preventive, predictive, or corrective—is critical for ensuring performance, reducing repair costs, and extending equipment life. A well-maintained generator guarantees reliable power supply during emergencies.
In the next blog, we will explore Periodic Maintenance of Generators: A-Check, B-Check & More. Stay tuned!
Comments